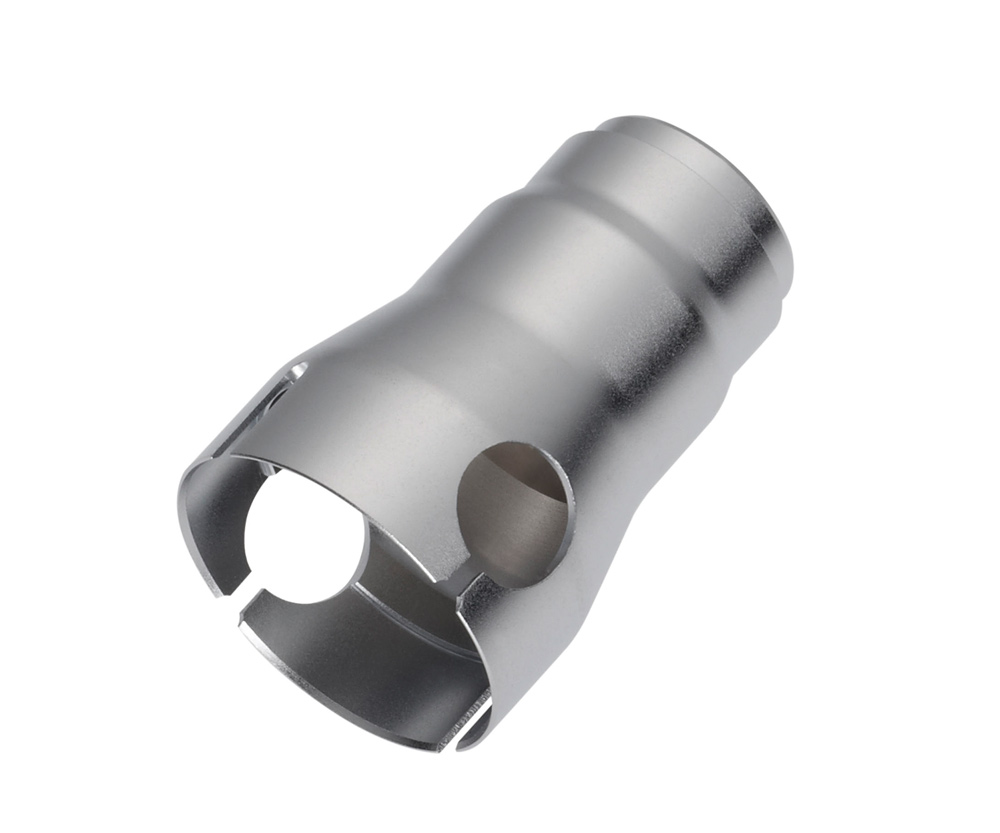
北京機械加工廠車床切削油霧潤滑技術優點和裝置
2024-04-11
北京精密機械加工廠常用的對刀方法:
一、采用尋邊器、偏心棒和軸設定器等工具對刀法:
操作步驟與采用試切對刀法相似,只是將刀具換成尋邊器或偏心棒。這是最常用的方法。效率高,能保證對刀精度。
機加工操作員使用尋邊器時必須小心,讓其鋼球部位與工件輕微接觸,同時被加工工件必須是導體,定位基準面有較好的表面粗糙度。z軸設定器一般用于轉移對刀法。
二、轉移對刀法:
加工一個工件常常需要用到不止一把刀,第二把刀的長度與第一把刀的裝刀長度不一樣,需要重新對零,但有時零點被加工掉,無法直接找回零點,或不容許破壞已加工好的表面,還有某些刀具或場合不好直接對刀,這時候可采用間接找零的方法。
1.對第一把刀
① 對第一把刀的時仍然先用試切法、塞尺法等。
② 把對刀器放在機床工作臺平整臺面上。
③ 手輪模式下,利用手搖移動工作臺至適合位置,向下移動主軸,用刀的底端壓對刀器的頂部,表盤指針轉動,最好在一圈以內,記下此時軸設定器的示數并將相對坐標軸清零。
④ 確抬高主軸,取下第一把刀。
1.對第二把刀。
①加工師傅 裝上第二把刀。
② 機械加工廠家操作人員在手輪模式下,向下移動主軸,用刀的底端壓對刀器的頂部,表盤指針轉動,指針指向與第一把刀相同的示數位置。
③ 記錄此時軸相對坐標對應的數值。
④ 抬高主軸,移走對刀器。
⑤ 將原來第一把刀的G5*里的z1坐標數據加上數,得到一個新的坐標。
⑥ 這個新的坐標就是要找的第二把刀對應的工件原點的機床實際坐標,將它輸人到第二把刀的G5*工作坐標中,這樣,就設定好第二把刀的零點。其余刀與第二把刀的對刀方法相同。
三、試切對刀法:
這種方法簡單方便,但會在工件表面留下切削痕跡, 且對刀精度較低。以對刀點(此處與工件坐標系原點重合)在工件表面中心位置為例采用雙邊對刀方式。
1. x,y向對刀。
① 將工件通過夾具裝在工作臺上,裝夾時,工件的四個側面都應留出對刀的位置。
② 啟動主軸中速旋轉,快速移動工作臺和主軸,讓刀具快速移動到靠近工件左側有一定安全距離的位置,然后降低速度移動至接近工件左側。
③ 靠近工件時改用微調操作(一般用0.01mm)來靠近,讓刀具慢慢接近工件左側,使刀具恰好接觸到工件左側表面(觀察,聽切削聲音、看切痕、看切屑,只要出現一種情況即表示刀具接觸到工件),再回退0.01mm。記下此時機床坐標系中顯示的坐標值。
④ 沿z正方向退刀,至工件表面以上,用同樣方法接近工件右側,記下此時機床坐標系中顯示的坐標值。
⑤ 據此可得工件坐標系原點在機床坐標系中坐標值。
⑥ 同理可測得工件坐標系原點在機床坐標系中的坐標值。
2.z向對刀。
① 將刀具快速移至工件上方。
② 啟動主軸中速旋轉,快速移動工作臺和主軸,讓刀具快速移動到靠近工件上表面有一定安全距離的位置,然后降低速度移動讓刀具端面接近工件上表面。
③ 靠近工件時改用微調操作(一般用0.01mm)來靠近,讓刀具端面慢慢接近工件表面,使刀具端面恰好碰到工件上表面,再將軸再抬高,記下此時機床坐標系中的z值,則工件坐標系原點W在機床坐標系中的坐標值。
3.將測得的x,y,z值輸入到機床工件坐標系存儲地址G5。
4.進入面板輸入模式(MDI),輸入“G5*”,按啟動鍵(在自動模式下),運行G5*使其生效。
5.檢驗對刀是否正確。
四、塞尺、標準芯棒、塊規對刀法:
這種方法與試切對刀法相似,只是對刀時主軸不轉動,在刀具和工件之間加人塞尺(或標準芯棒、塊規),以塞尺恰好不能自由抽動為準,注意計算坐標時這樣應將塞尺的厚度減去。因為主軸不需要轉動切削,這種方法不會在工件表面留下痕跡,但對刀精度也不夠高。